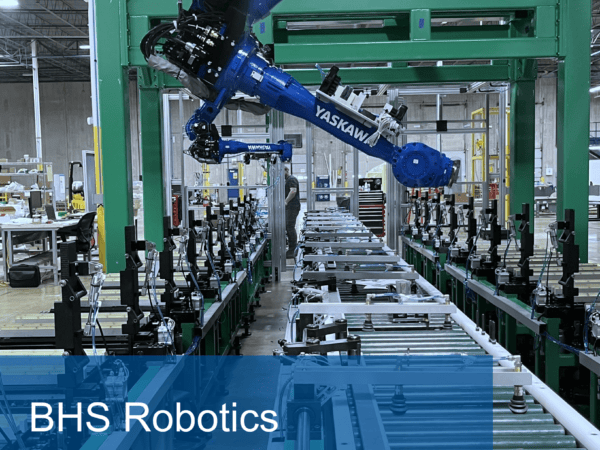
PROJECT SUMMARY
Using two robots working in tandem, BHS Robotics developed a unique solution for handling and stacking of custom steel roof panels.
THE CHALLENGE
Corrugated roofing materials are very large and thin. Handling these materials is challenging due to the ergonomics of the task and also due to the risk of bending or twisting the product if it is not supported properly. This manual approach is slow and remaking damaged pieces is a detriment to the throughput of the facility.
THE SOLUTION
A material list is prepared by the designer based on the lengths of number of panels needed for the customers’ order. A material list will include many different panel sizes from 4’ to 35’ to outfit the specific roof.
The process begins with the rolls of steel entering the roll-forming machine to produce the ridges needed for the roofing material. After forming the metal, the steel is cut to the lengths necessary for the customer order. The individual panels are then conveyed into the packaging solution.
BHS Robotics designed and built a custom system which applies two inverted robots to stack panels using a coordinated motion program. Shorter panels will be picked up using a vacuum tool by one of the robots and moved to the stacking area. Longer panels will be picked up by both robots simultaneously to support the product across its length, without bending or twisting the material.
The formed stack is manually strapped and then conveyed out of the cell for transport to the shipping area.
IMPACT TO THE CUSTOMER
Throughput of the system has been increased significantly because the packaging area can now keep pace with the roll forming machine. Handling the material using the tandem robots has significantly reduced damage during the packaging process which ensures orders get completed efficiently on the first pass.
Operators are now removed from the strenuous task of handling these large materials which alleviates fatigue and risk of injury at this facility.
BHS Robotics is a leading expert in robotic handling of heavy-duty materials such as corrugate, steel, glass, drywall and other specialty building products. Whether your facility is working with rolls, board or sheets, contact us to learn how BHS Robotics can add value to your business with automation!