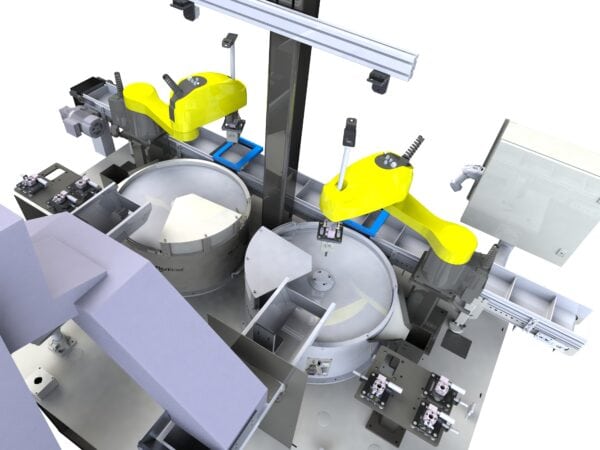
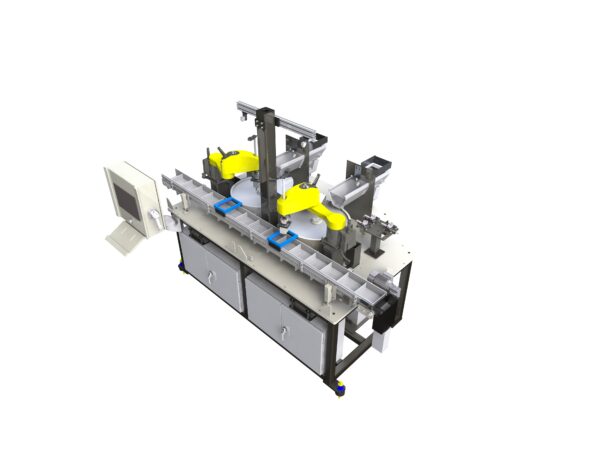
PROJECT SUMMARY
BHS Robotics has developed an innovative vision-guided solution for efficiently sorting and picking of multiple SKU’s on one machine. BHS has integrated these solutions for aftermarket parts kitting, assembly systems, and sortation.
THE CHALLENGE
A global manufacturer of construction equipment came to BHS for assistance in automating a spare parts kit assembly process. The kit contains nuts, bolts and other fastener hardware.
The customer has over 150,000 unique SKUs that can run through the system. The variety of parts created challenges with their existing feeder bowl systems due to difficult changeovers and low flexibility.
THE SOLUTION
BHS developed a compact robotic work cell with a flexible vision system capable of handling parts with varying form factors, at 80-90 picks per minute. The vision system allows the customer to make adjustments during product change overs. This customer was so satisfied with the solution, they ordered three more duplicate systems.
The machine operator loads the bulk hopper elevator with the appropriate parts. The hopper elevator then transports these components to one of two prefeeders. These prefeeders supply parts to the vision pick area for identification and location.
The Keyence vision system communicates part location data to the FANUC SR-6iA for picking. The robot acquires one part at a time from the pick area and places it onto the transport conveyor.
Gripper changeover is incorporated into the system to facilitate automatic changeover for a wide variety of part types and geometries.
The conveyor transports the parts to an automatic bagging or cartoning machine, depending upon the packaging requirements.
IMPACT TO THE CUSTOMER
Robotic Flexibility: The system is preconfigured to handle a wide variety of component types based on SKU’s selection from the operator screen.
High Throughput: Achieves 80-90 picks per minute.
SKU Handling: System is designed to be able to process an unlimited number of SKUs.
Enhanced Efficiency: Consistent throughput without stoppages for 3 shifts per day. Can run unattended during off shifts.
Automatic Tool Changing: Enables seamless transitions between different component types.
BHS Robotics specializes in the application of advanced vision technologies and robotics to provide flexible processing solutions for high mix environments our clients. Contact us to learn more about how BHS Robotics can add value to your business with flexible automation!